روش های ساخت محصولات
روشهای ساخت محصولات – نحوه شکل دهی و به وجود آوردن محصول یا قطعه مورد نظر را گویند که بر اساس مواد مختلف ، روش های مختلفی در نظر گرفته می شود . در اینجا مهمترین روش های ساخت قطعات پلاستیکی و فلزی آورده شده که شامل مواردی چون اکستروژن ، خم کاری ، واترجت ، ریخته گری ، قالبگیری تحت خلا ، قالبگیری دمشی ، قالبگیری تزریقی و قالبگیری چرخشی است .
آشنایی با روش های ساخت محصولات اهمیت زیادی دارد
نسبت به دقت و کیفیت قطعه و محصول میتوان روش ساخت بهینه را تشخیص داد .
با انتخاب بهینه روش ساخت می توان با هزینه های کم تر و در زمان کوتاه تری ، قطعه و محصول را تولید کرد به همین منظور روش ساخت بیشترین تاثیر در تعیین قیمت تمام شده محصول را دارد و در نهایت کمک زیادی برای رقابت در بازار به فروش می کند از این بابت برای سرمایه گذاران اهمیت زیادی دارد .
مجموعه مثلث طراحی
مهندسین مجموعه به همراه طراحان این مجموعه در کنار شما هستند تا با مشاوره در زمینه نحوه ساخت به شما کمک کنند در کوتاه ترین زمان و با کمترین هزینه قطعات و محصولاتتان را با طراحی های پیچیده و چشم گیر به بازار ارائه کنید و در رقابت بازار فروش محصولات سهم بزرگی را از آن خود کنید . مشاوره مجموعه مثلث طراحی کاملا رایگان بوده و میتوانید با تماس و ارسال نمونه برای ما ، از روش ساخت و مدت زمان و هزینه های ساخت قطعه – محصول – بسته بندی آگاه شوید .
ماشینکاری
روش های ساخت محصولات توسط ماشینکاری
ماشینکاری قطعات از رایج ترین روش های شکل دهی و ساخت قطعات بوده و با استفاده از نیروی حرکتی و ابزار براده برداری ، قطعات شکل دهی می شوند .این نیروهای حرکتی باعث تفاوت در نوع ماشینکاری می شود بطور مثال حرکت خطی (صفحه تراش ) – حرکت چرخشی قطعه ( ماشین تراش ) – حرکت چرخشی ابزار ( ماشین فرز ) و …
اکستروژن
روش های ساخت محصولات توسط اکستروژن
اکستروژن(Extrusion) یک از روش های ساخت و تولید است و برای تهیه قطعات ادامه دار مانند میله ، لوله ، شیلنگ ، ورق های نازک ، لاستیک دور در خودرو ، الیاف شیشه ، ماکارونی ، پروفیل درب و پنجره ساختمان و پروفیل قاب عکس مورد استفاده قرار می گیرد . در این شیوه ماده مذاب یا نیمه سیال جهت شکل گرفتن به فرم دلخواه با فشار از یک قالب عبور داده می شود و پس از خروج خنک می گردد تا شکل آن تثبیت شود . در واقع روش اکستروژن را می توان به صورت ساده شبیه محفظه خروجی چرخ گوشت در نظر گرفت .
نوردکاری
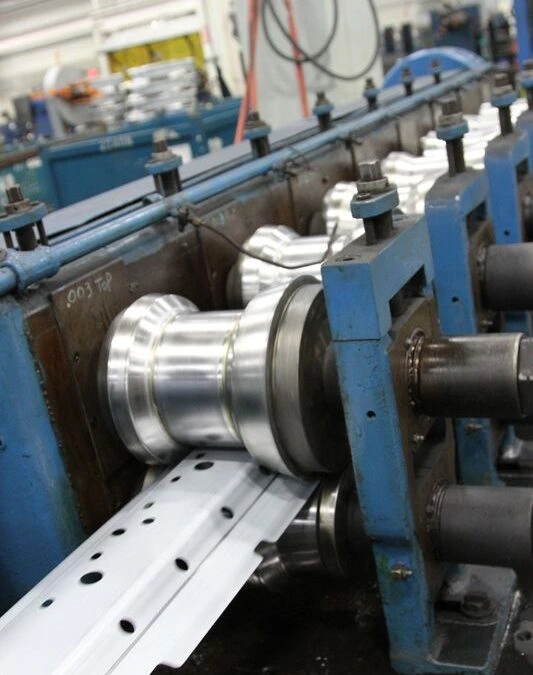
روش های ساخت محصولات توسط نرودکاری
نوردکاری به شکل دهی ماده خام اولیه در جریان عبور از میان تعدادی غلتک دوار اتلاق می شود . یکی از کاربردهای عمده این روش در تهیه مقاطع استاندارد نظیر ورق ها و تسمه ها در کارخانه های ذوب فلزات است . از شیوه نوردکاری می توان برای کاستن از ضخامت ورق نیز استفاده کرد ، بدین صورت که در حین فرآیند ، اعمال نیرو توسط غلتک های دوار ، از سطح مقطع ورق کاسته شده و گسترده می شود .
خم کاری (Bending)
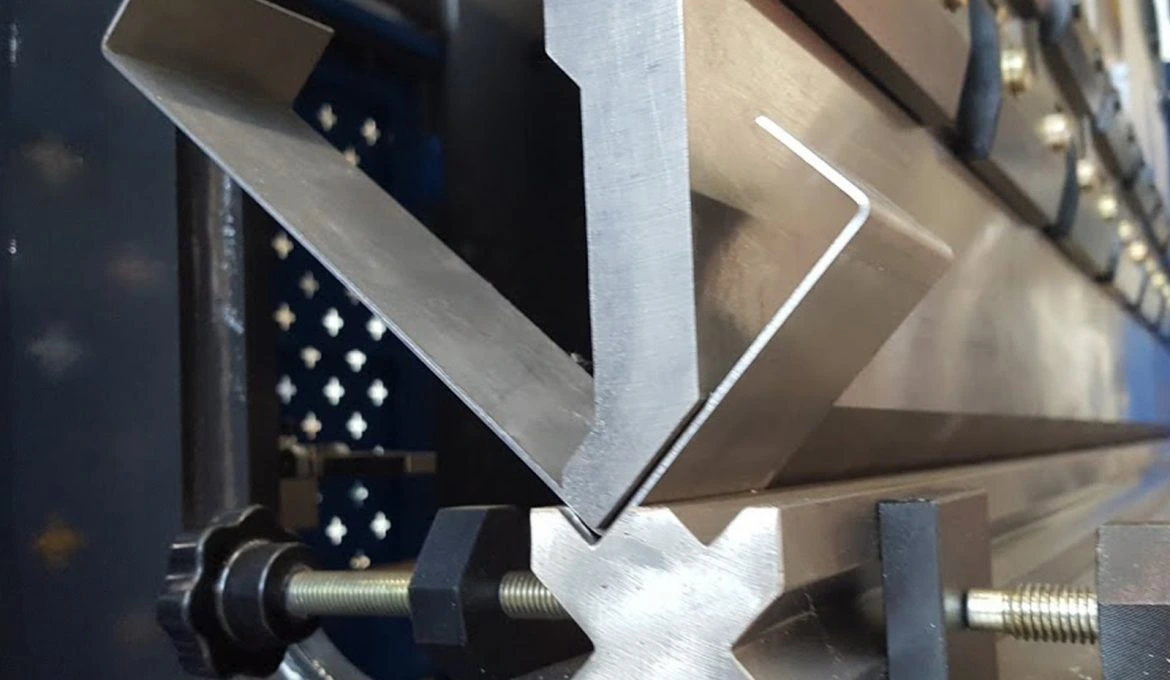
روش های ساخت محصولات توسط خم کاری
در خم کاری و شکل دهی لوله و دیگر قطعات توخالی ، به تکیه گاهی داخلی نیاز است که مندرل (mandrel) نامیده می شود و از چین خوردن و پیچ خوردن لوله طی فرآیند خمش جلوگیری می کند .
واترجت
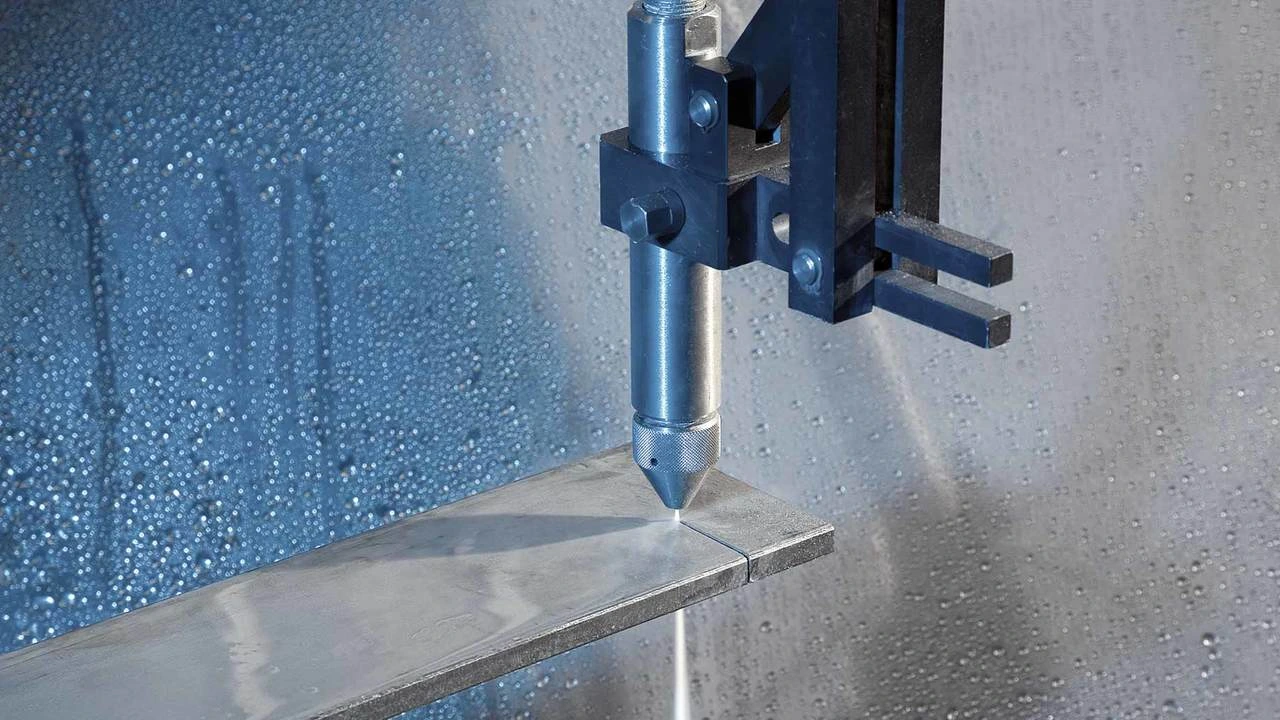
روش های ساخت محصولات توسط واترجت
دستگاه برش تمامی مواد با استفاده از فشار بالای آب می باشد . آب با خروج از نازلی با قطری خیلی کوچک در ترکیب با مواد ساینده می تواند هر ماده ای را برش دهد .
ریخته گری (Casting)
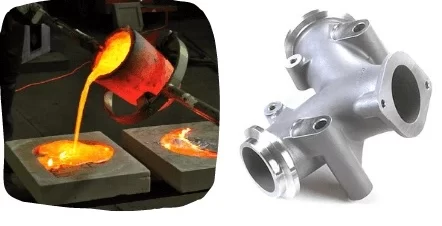
روش های ساخت محصولات توسط ریخته گری
یکی از روش های ساخت و تولید قطعات است و به لحاظ نحوه عملکرد ، مشابه قالبگیری تزریقی است ولی بیشتر در مورد فلزات غیر آهنی مانند آلومینیم ، سرب و روی کاربرد دارد . فن شکل دادن فلزات و آلیاژ ها از طریق ذوب ، ریختن مذاب در محفظه ای به نام قالب و آنگاه سرد کردن و انجماد آن صورت می گیرد . ریخته گری برای تولید انبوه قطعات کوچک و متوسط که دارای جزییات ، پیچیدگی و یا سطح مقطع نازک بوده و از کیفیت سطحی و ثبات ابعادی مناسبی برخوردارند ، مطلوب است دو روش در ریخته گری شامل ریخته گری تحت فشار و ریخته گری دوغابی می باشد .
قالب گیری تحت خلا
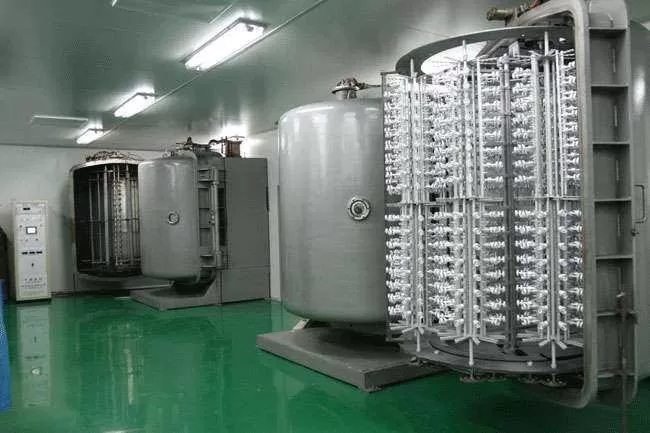
روش های ساخت محصولات توسط قالب های خلا
قالب گیری تحت خلا یا وکیوم فرمینگ (Vacuum forming) شیوه ای است که با بهره گیری از کاهش فشار هوا و ایجاد خلا از یک سو و فشار معمولی هوای محیطی از سوی دیگر به شکل دهی ماده درون قالب می پردازد .
قالب گیری دمشی (Blow molding)
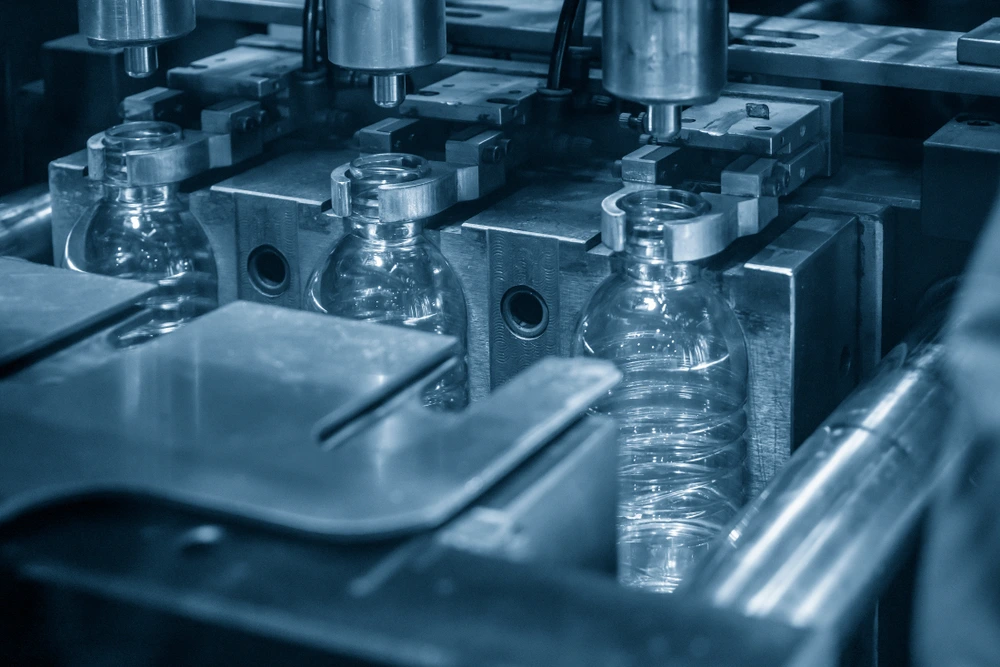
روش های ساخت محصولات توسط قالبگیری دمشی
قالبگیری دمشی یا بادی روشی است که طی آن ماده شکل پذیر نیمه سیال مانند پلاستیک گرم شده و به واسطه ورود هوای فشرده به داخل آن باد می شود و لایه نازکی را تشکیل می دهد که این لایه به دلیل محدود بودن فضای درون قالب شکل آن را می گیرد ، پس از سرد شدن قطعه و تثبیت شکل آن ، از قالب خارج می شود.
این روش تولید ، معمولا برای تهیه قطعات میان تهی مانند بطری به کار می رود .
قالب گیری تزریقی
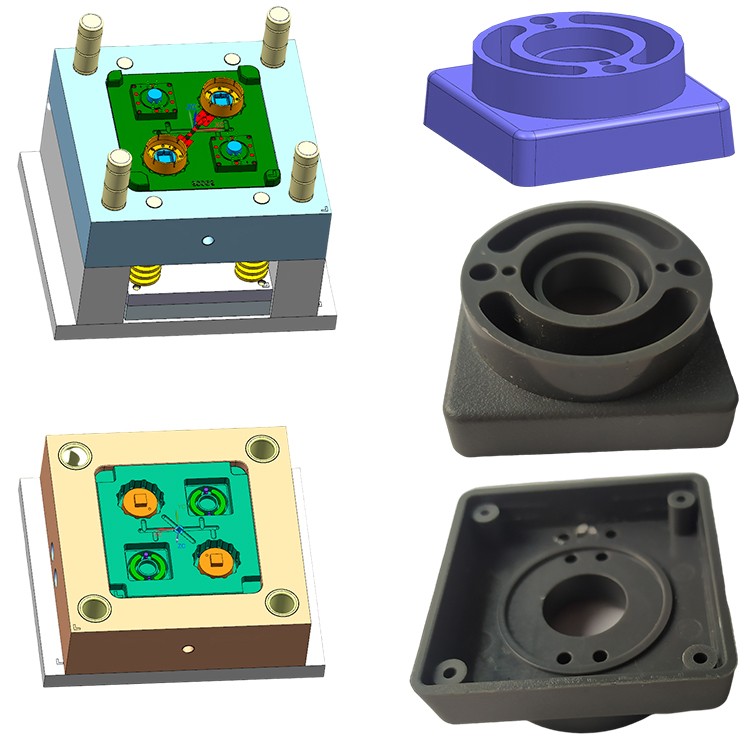
روش های ساخت محصولات توسط قالب گیری تزریق
شاید هیچ فرآیندی به اندازه قالب گیری تزریقی ، طراحی صنعتی را متحول نکرده باشد . این فرآیند بر پایه فناوری ریخته گری با محفظه داغ برای فلزات به وجود آمد ، اما پیشرفت های اخیر حاصل شده در این فرآیند و نیز پیشرفت مواد پلیمری ، به طراحان آزادی عمل وسیعی بخشید .
شیوه تزریق ، یکی از روش های شکل دهی مواد سیال در قالب صلب است و امروزه کاربرد گسترده ای در شکل دهی قطعات ساخته شده از پلاستیک ها دارد . در این روش ابتدا سیال با فشار زیاد از طریق راهگاه وارد محفظه قالب می شود . این فشار توسط قطعه مارپیچ دستگاه تزریق ، به وجود می آید . تعداد قطعات قالب ، بسته به میزان پیچیدگی قطعه نهایی متفاوت است لیکن اصول کلی قالب سازی در مورد قطعات آن صدق می کند . لازم است سطوح قطعات قالب نسبت به هم ، شیب منفی نداشته و ترجیحا از هر طرف حداقل به اندازه چند درجه بیشتر از حالت قائم باشند . لبه های این سطوح در محل اتصال به یکدیگر باید کمی گرد شوند تا قطعه پس از شکل گیری ، به آسانی از قالب جدا شود .
قالب گیری چرخشی
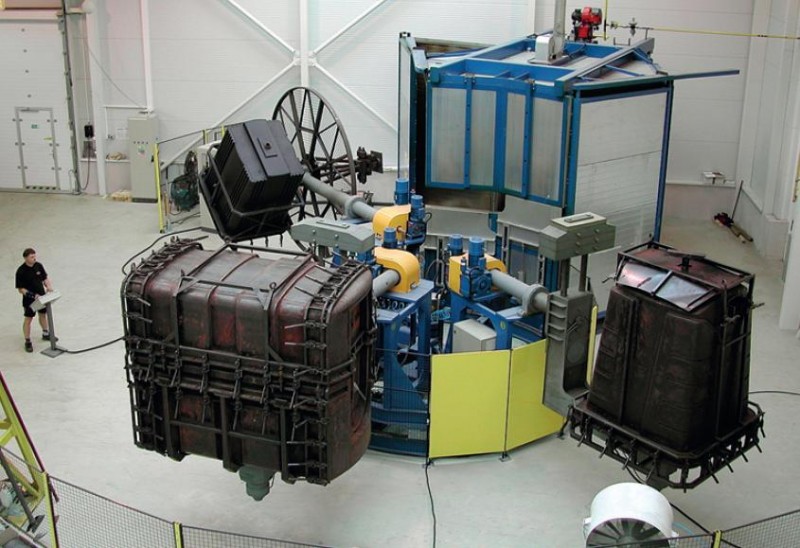
روش های ساخت محصولات توسط قالب گیری چرخشی
یکی از روش های شکل دهی قطعات است و بیشتر برای تهیه محصولات بزرگ و توخالی پلاستیکی به کار می رود . اساس کار به این صورت است که ابتدا مقدار مشخصی از مواد اولیه پلیمری که اغلب به صورت پودر می باشند ، وارد قالب می شوند . سپس قالب گرم شده و حول حداقل دو محور شروع به چرخش می کند . مواد به واسطه دریافت گرما ذوب شده و بر اثر حرکت دورانی دستگاه ، لایه نازکی بر روی بدنه قالب تشکیل می دهند . پس از گذشت مدت زمان معین ، در حالی که هنوز قالب در حال چرخش است آن را سرد می نماید تا شکل قطعه تثبیت شود . در نهایت محصول از دستگاه خارج می گردد. بدنه قایق ها ، وسایل نقلیه تفریحی ، تانک ها ، ظروف زباله و دیگر محصولات مشابه با این روش تولید می شوند . نام دیگر این روش دورانی است .
پرینتر های سه بعدی فلزات و پلاستیک
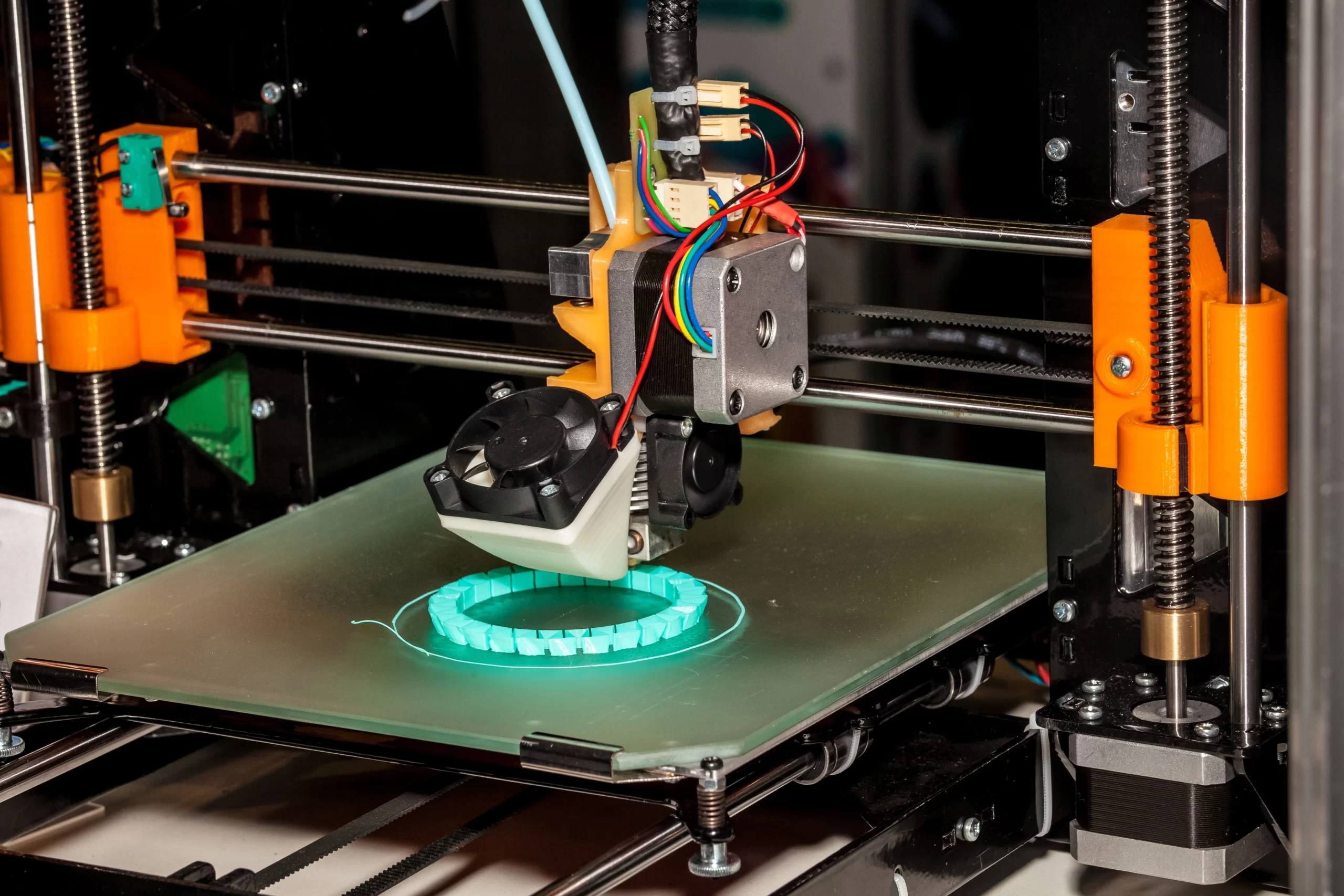
روش های ساخت محصولات توسط پرینتر های سه بعدی
پرینتر ها دارای نازل هستند که با حرکت نازل در سه محور مختصاتی ، ذوب و تزریق همزمان مواد ، لایه هایی را رو هم میچیند که در نهایت شکل قطعه طراحی شده پدید می آید . مواد مورد استفاده در پرینترها برای تولید قطعات می تواند در دو نوع انعطاف پذیر و سخت باشد .