شکل دهی پلاستیک و پلیمر
شکل دهی پلاستیک و پلیمر ، مجموعه مثلث طراحی سازنده انواع قالب های تزریق جهت شکل دهی پلاستیک و پلیمر در راستای استفاده محصول نهایی
از طراحی تا مدل سازی سه بعدی ایده ها و نهایی سازی طرح سه بعدی و ساخت قالب تزریق انواع پلیمر ها
شکل دهی پلیمرها
از میان عوامل متعددی که سبب افزایش سریع کاربرد پلیمرها شده است ، دو عامل از همه مهتر است . نخست ، وجود یک سلسله ویژگی های ذاتی جالب از قبیل سبکی ، ارزانی ، چقرمگی ، مقاومت در برابر خوردگی و … آنهاست . دوم ، سادگی ، روان بودن و سرعت عملیات شکل دهی آنهاست که پلیمر خام را به اشیای قابل استفاده تبدیل می کند .
مهمترین عملیات شکل دهی در مورد پلاستیک ها عبارت است از قالبگیری تزریقی و اکستروژن .
در این دو روش نخست پلیمر گرم می شود تا به حالت مایع در آید ؛ سپس تحت یک فشار خاص (غالبا بسیار زیاد) به شکل مورد نظر در آورده شده سپس سرد می شود تا جامد گردد . ساده ترین روش ، اکستروژن است . یک اکسترودر در واقع یک چرخ گوشت ، بزرگ و داغ است که توسط یک موتور چرخانده می شود . گرانول های سرد پلیمر به درون قیف وارد شده ، نیروی ثقل آنها را به طرف مارپیچی که در داخل یک استوانه داغ به جلو رانده می شود . این گرانول ها در داخل استوانه بین تیغه های مارپیچ و دیواره داغ استوانه به جلو رانده می شود . با حرکت در داخل اکسترودر ، پلیمرهای بلورین با عبور از نقطه ذوب و پلیمرهای آمورف با عبور از نقطه شیشه ای به مایع تبدیل تبدیل می شوند . پلیمر مایعی که اینک تحت فشار نیز قرار دارد ، پس از عبور از اکسترودر به یک حدیده که نخستین قسمت سیستم شکل دهی است می رسد .
عملیات تزریق در ماشین های تزریق پلاستیک
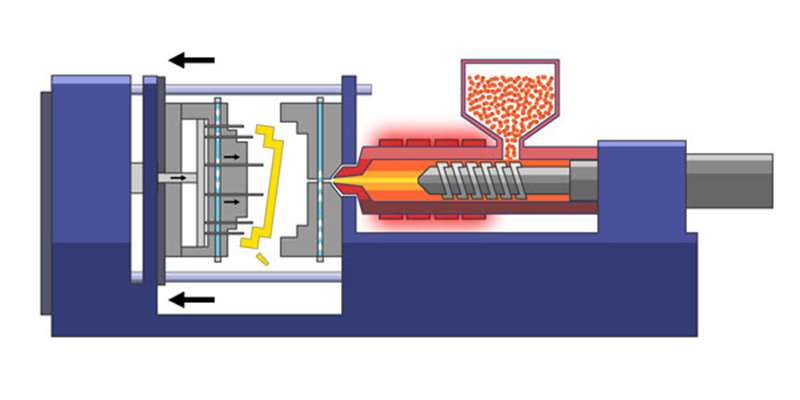
شکل دهی پلاستیک و پلیمر
مارپیچ پیش نرم کننده در اصل یک اکسترودر است که مذاب را به استوانه دوم وارد می سازد . در حین انجام این عمل ، پیستون تزریق در مقابل یک فشار برگشتی کنترل شده به عقب رانده می شود . هنگامی که اندازه مطلوب تزریق فراهم آمد ، شیر مبدل استوانه تزریق جلو آمده مایع را به داخل قالب تزریق می کند .
از آنجا که پلیمر مذاب بسیار ویسکوز است ، نیروی بزرگ تر f1 لازم است تا پیستون را به سرعت به جلو برده و مایع را از میان کانال های بسیاری به درون قالب ، فشار دهد . همچنین نیروی بزرگتر f2 لازم است تا قالب را در حین تزریق بسته نگه دارد . سپس مبدل مجددا می چرخد تا قالب را جدا کرده و مارپیچ پلاستیک ساز استوانه تزریق را پر کند . در حین این عمل قطعه قالبگیری شده سرد می شود و قسمت های متحرک قالب کنار رفته و قطعه خارج می گردد و قالب مجددا برای قالبگیری بسته می شود . استوانه تزریق می تواند هم بصورت موازی با استوانه تزریق و هم بصورت زاویه دار با آن باشد . مدت زمان یک چرخه کامل به عوامل زیادی بستگی دارد .
خواص مهم پلیمر مذاب که در این عملیات مورد توجه هستند ، در سوالات زیر خلاصه شده است
- ویسکوزیته برشی پلیمر مذاب و همچنین دما وسرعت به چه عواملی بستگی دارد ؟
- ویسکوزیته طولی و مقاومت طولی پلیمر مذاب چیست ؟
- مذاب بتواند تنش های کششی را تحمل کند ، متعاقبا این تنش های کششی و همچنین برشی می توانند در پلیمر مذاب که به ظروف بسته جاری می شوند به وجود آیند . این مسئله در جریان مذاب چه تاثیری خواهد داشت ؟
- هنگامی که پلیمر مایع در قالب ، جامد می شود در شرایط غیر متعارف قرار دارد . به وجهی که مذاب تحت یک سری تنش های برشی و کششی که نمی توانند تا صفر آسایش یابند ، قرار می گیرد . متبلور شدن در این شرایط بر ساختمان ظریف و خواص محصول چه اثری می تواند داشته باشد .
انواع جریان ها در مذاب پلیمری
- جریان طولی
- جریان برشی ساده
- جریان مذاب تحت فشارهای هیدرواستاتیکی
طراحی برای تولید
در انتخاب مواد پلیمری تصمیم گیری همزمان بر روی روش ساخت قطعه و در نظر داشتن اثرات فرایند بر خواص بسیار مهم است . در حالی که قطعات فلزی توسط یک سری از عملیات شامل آهنگری ، پرس ، ماشین کاری ، عملیات حرارتی ،و صیقل کاری ساخته می شوند ، قطعات پلیمری معمولا در یک مرحله شکل می گیرند و برای عملیات بعدی فرصت کمی در اختیار است . یک طرح بر روی تخته طراحی ممکن است بسیار جالب به نظر آید ، ولیکن به علت عدم توجه کافی به فرایند تولید می توان ناموفق باشد . پیش از این که به بحث های متداول طراحی در زمینه سفتی و استحکام بپردازیم ، ضروری است در مورد اثرات جزییات روش تولید بر کارایی محصول صحبت کنیم .
پلیمرها در ویژگی های فرآیند با یکدیگر بسیار متفاوت اند ؛ و ضروری است که اطمینان حاصل شود که طراحی به عمل آمده به طرز موفقیت آمیز و اقتصادی می تواند از مواد انتخاب شده به تولید برسد . بارزترین اختلاف ها در رفتار فرآیند گرما نرم ها و مواد مرکب دارای الیاف بلند د یده می شود ؛ ولیکن اختلاف های مهمی در هر دسته از پلیمر ها نیز وجود دارد . به عنوان مثال ، PTFE آن چنان ویسکوزیته مذاب بالایی دارد که نمی توان آن را قالبگیری تزریقی نمود و باید آن را بصورت پودر با روش زینتر شکل دهی کرد . اختلاف عا میان ویسکوزیته مذاب ، بلورینگی و مقاومت در برابر تاب خوردگی در اثر قالب تحت تنش ، عواملی هستند که باید در ایجاد یک طرح در نظر گرفت . مسلما مسائل اقتصادی نیز در این میان مهم هستند . هنگامی که تولید یک قطعه به صورت انبوه مطرح است ، قالبگیری تزریقی معمولا فرایند برتر است . شکل دهی گرمایی نیز هنگامی که کاهش هزینه سرمایه ای در ماشین آلات و قالب ها بر هزینه اضافی به اکسترود کردن ورقه ها پیش از شکل دهی غلبه کند ، یک فرایند مهم به حساب می آید ولی تنها برای تولید اشکال نسبتا ساده مناسب می باشد . عامل دیگری که در ارائه یک طرح باید در نظر گرفت ، چگونگی اتصال قطعه به سایر قسمت های محصول است . در مورد گرما نرم ها جوشکاری و فرایند چفت کردن مناسب است ، در حای که رزین های گرما سخت را نمی توان جوشکاری کرد و باید با استفاده از چسب و چفت کردن مکانیکی ، قطعات را به یکدیگر متصل نمود .
قالبگیری تزریقی
طراحی قالب اصلی ترین قسمت فرایند طراحی است . یک قالب پیچیده به اندازه یک منزل مسکونی بزرگ ارزش دارد و پس از این که ساخته شد به میزان اندکی قابل تغییر است . اگر مشکلات جدی پیش آید ، آنگاه بایستی قالب کنار گذاشته یک قالب جدید ساخت . دو مساله مهم مربوط به محل A خط مشترک دو نیمه قالب و AA دروازه ، یا دروازه ها می باشد . روش های خارج سازی قطعه قالب گیری شده پس از اتمام قالبگیری نیز نیاز به اندکی تامل دارد . خارج سازی قطعه با قرار دادن یک زاویه انحراف به اندازه’ 1.8 تا 1’ که بستگی به سفتی مواد دارد و با استفاده از میله ها یا صفحات خارج کننده انجام می گیرد . قطعاتی که حاوی برش ها و حفره های عرضی هستند ، احتیاج به تعدادی هسته های انقباض پذیر دارند که مسلما سبب افزایش قیمت می شود . شیارهای داخلی و خارجی را نیز می توان به همین روش ، با استفاده از میله های هسته ای که نمی توانند بچرخند ، به وجود آورد . به روش دیگر ، قسمت های برش ، شامل شیارهای خارجی را می توان از روی قالب بریده و یا برداشت ، به شرط آن که کرنش های ایجاد شده در فرآیند از حد مجاز تجاوز نکند . انجام این روش در مواد تقویت شده با شیشه توصیه نمی شود ، زیرا که کرنش های وادادگی آنها پایین است .
روشی که با آن قالب پر می شود تعیین کننده جهت ، میزان و نوع جهت گیری مولکولی در قطعه قالبگیری شده به خصوص در نزدیکی سطح می باشد .
قالبگیری بادی
شکل دهی پلاستیک پلیمر بصورت بادی
قالبگیری بادی یک روش پر مصرف برای تولید ظروف توخالی (عموما بطری ها ) در مقیاس بزرگ و بسیار ارزان قیمت می باشد . سه نوع عمده از این روش وجود دارد :
- قالبگیری بادی اکستروژن
- قالبگیری بادی تزریقی
- قالبگیری بادی کششی
در تمام این روش های شکل دهی پلاستیک پلیمر بصورت بادی ، نخست یک پیش رو که تیوب توخالی ساده به نام (parsion) است تشکیل می گردد . یک انتهای parsion بسته است (اندکی فشرده شده است) به نحوی که می توان آن را در حالت گرم و نرم شده باد کرد . parsion تا جایی باد می شود که به دیواره قالب سرد بچسبد . در یک لحظه parsion شکل قالب را به خود گرفته و سرد می شود . سپس قالب باز شده و بطری خارج می گردد .